Topic specialists and trade stakeholders define some efficient strategies for bringing down the price of electrical car manufacturing. By Will Girling
Electrical autos (EVs) are arguably higher than they’ve ever been: customers now have entry to a higher number of fashions at completely different worth factors and vary capabilities to go well with their wants. Nonetheless, manufacturing these merchandise profitably has been an ongoing problem for automakers. Few are working within the black, and a few are seeing mounting losses from their EV actions.
Commerce wars, geopolitical shifts, and slower-than-anticipated uptake have all conspired to make EV manufacturing tougher and costly than many initially anticipated. Q1 2025 experiences from Volkswagen and Ford point out they nonetheless lose hundreds of {dollars} per EV offered. In the meantime, even people who have made progress face worsening circumstances: Normal Motors’ EV line-up was lastly “variable revenue optimistic” in This autumn 2024, however US import tariffs may reshape key provide chains and push prices again up once more.
In an more and more unstable world market, all automakers have to know the place and the way they’ll get monetary savings all through the EV manufacturing course of. Automotive World requested trade stakeholders and topic specialists to determine among the greatest alternatives for value reductions.
Reimagine manufacturing
Giacomo Margiotta-Mills, Transportation & Mobility Trade Director for Northern Europe at simulation software program firm Dassault Systèmes, says: “The full manufacturing value of an EV may be segmented into R&D, manufacturing, and re-use. Whereas separate, they’re additionally inherently interconnected.
“R&D for EVs is presently very costly and time-consuming for a lot of Western automakers, typically three to 5 years, and there’s dialogue about easy methods to study from Chinese language manufacturers undertaking it in 18-24 months. That’s an enormous value saving in itself, and modularity by means of multi-vehicle platform architectures might help reign within the manufacturing prices of EVs and software-defined autos even additional. It brings economies of scale, effectivity, and the power to re-use sources throughout a variety of autos.
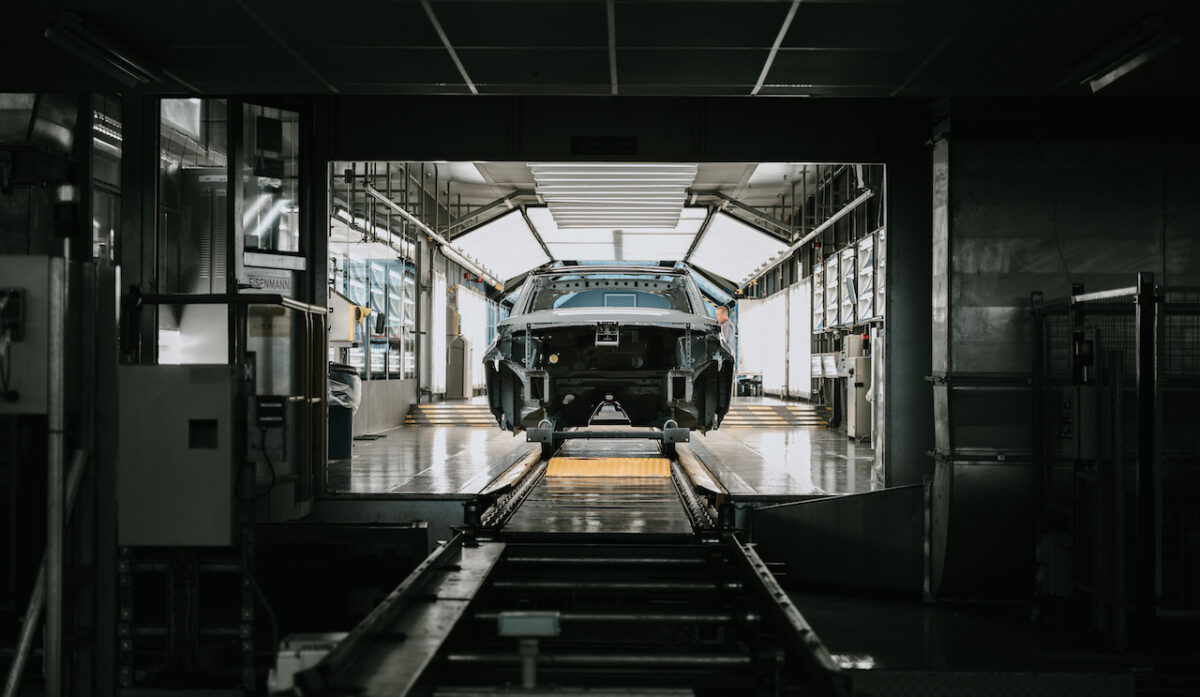
“Digital twins mixed with synthetic intelligence (AI) are the frequent threads that may carry all of this collectively in EV manufacturing. The battery is usually as much as 40% of a car’s whole value, so utilizing virtualisation to optimise in line with particular strategic targets—security, sourcing, efficiency—mitigates the excessive expense of real-world testing. With AI skilled to determine the best chemistries to fabricate and the way a cell will carry out all through its life, together with second-life functions, automakers can produce EVs cheaper but additionally higher.
“These value financial savings will originate in battery manufacturing initially, however I count on to see the identical pondering utilized all over the place ultimately. Corporations utilizing our 3DExperience platform, equivalent to Jaguar Land Rover, are utilizing digital twins in a wider and extra formidable manner than producers have achieved earlier than.”
Think about new supplies
Vincent Ledoux Pedailles, Chief Business Officer at battery anode producer CarbonScape, says: “As automakers look to chop EV manufacturing prices, many are nonetheless struggling to take action in a manner that’s each financially viable and environmentally sustainable. A lot of the problem stems from expensive battery supplies and sophisticated world provide chains closely dominated by China, but few corporations are exploring alternative routes to supply the essential minerals wanted for EV batteries.
“Biographite, a carbon-negative various for the lithium-ion anode market, which may be made domestically from woodchips, could possibly be key to fixing this problem. Past the environmental advantages, it gives producers an opportunity to decrease manufacturing prices because of a available, low-cost biomass feedstock. With out compromising on efficiency, biographite additionally helps automakers keep away from commerce dangers and cut back import and freight bills.
“Finally, by embracing domestically sourced battery supplies, automakers received’t simply increase long-term resilience and value effectivity, they’ll additionally carry key elements of EV manufacturing again house, contributing to a extra sustainable future.”
Increase high quality management
Philippe Arsonneau, Senior Vice President of Infrastructure and Energy Methods at power administration and automation specialist Schneider Electrical, says: “Traditionally, the battery pack represents the lion’s share of an EV’s value. Compounding this, present mature battery factories face important scrap charges, starting from 6% to fifteen%, as a result of high quality points detected late within the course of. For newer entrants, these figures may be significantly greater. Addressing this head-on gives a direct and substantial lever for value discount.
“Integrating superior AI-powered high quality management all through the battery manufacturing course of can allow real-time defect detection and prevention. This implies fewer defective cells, diminished materials waste, and in the end, decrease battery prices. This deal with ‘first-time-right’ manufacturing is paramount in making EVs extra inexpensive.
“Past optimising the manufacturing course of itself, one other essential space for OEMs to prioritise is implementing superior predictive upkeep methods throughout their manufacturing operations. Unplanned downtime is a major value driver in any industrial setting, and EV manufacturing isn’t any exception.
“Distant monitoring, professional evaluation, and predictive algorithms can anticipate potential gear failures earlier than they happen. This condition-based upkeep strategy can drastically cut back electrical failure dangers by as much as 75% and minimize unplanned downtime and on-site actions considerably—by as a lot as 40%. By making certain steady operation and minimising disruptions, OEMs can obtain substantial value financial savings and enhance general effectivity.”
Prioritise environment friendly manufacturing
Emile Naus, Companion at administration consultancy BearingPoint, says: “Producers have to do all the things they’ll to make extra EVs extra effectively. The primary value issue continues to be batteries, so decreasing their weight and expense whereas enhancing efficiency will yield the quickest financial savings. Reaching these may imply rethinking whole EV designs, however the optimistic is that even minor tweaks can snowball. For instance, altering aerodynamics barely may imply diminished general energy consumption and subsequently smaller, lighter, and cheaper batteries.
Producers have to do all the things they’ll to make extra EVs extra effectively
“Effectivity additionally applies to how automakers leverage partnerships with their suppliers. Put merely, if one thing isn’t essential to the shopper’s direct expertise of a model, OEMs ought to discover alternatives for collaboration. Elementary choices embody the chassis, battery, and drivetrain. The extra prices may be shared throughout an ecosystem, the cheaper every car will probably be to provide, significantly if developed on multi-vehicle platforms.
“By way of streamlining manufacturing itself, gigacasting has promise nevertheless it’s not the one resolution accessible. EVs have fewer elements and might subsequently be made on simplified manufacturing traces which might be simpler to automate. Among the section leaders provide restricted personalisation choices, opting to focus extra on software-driven differentiation as a substitute of {hardware}. This opens up loads of new income alternatives, and EVs which might be designed to last more by means of common software program updates may cut back manufacturing prices just by producing fewer autos.
“Nonetheless, whereas software program may assist automakers get monetary savings producing EVs, there’s a large cultural problem connected. They might want to settle for a brand new regular of promoting fewer autos at the next worth and with an extended lifespan, throughout which manufacturers can constantly generate new worth. Messaging to shareholders would have to be fastidiously thought of.”
Give attention to power
James Crosby-Wrigley, Head of Sustainability at power specialist Benefit Utilities, says: “OEMs are experiencing quite a lot of issues past their direct management, together with import tariffs and the wholesale prices of uncooked supplies. It’s essential for corporations to deal with what they’ll affect instantly; not essentially manufacturing processes, however quite the general effectivity of manufacturing unit infrastructure.
“Vitality—electrical energy, fuel, and so on.—is often the third-highest value of manufacturing, and audits may be carried out to find out the place financial savings may be made. For instance, has manufacturing unit lighting been switched to LEDs, or can the carried out metering options successfully decide how power is distributed across the website? Asking these sorts of questions can determine low-hanging fruit within the first occasion, like out-of-hours power wastage and alternatives for decreasing idle time. Going ahead, corporations can pursue higher power self-sufficiency by incorporating proximate photo voltaic panels, wind generators, and hydrogen electrolysers. Present estimates recommend roughly 25-30% of an OEM’s power could possibly be self-generated utilizing renewable power.
“Following these options will at all times assist make manufacturing cheaper, significantly throughout instances of unstable power costs. A comparatively inefficient website may see enhancements of 35-40%. As extra automakers deal with power effectivity, I feel we may see extra exercise in self-generated clear power tasks for factories.”